Our Mission
Design, manufacture, and deliver the ultimate lighting solution.
Vision X Lighting is located in Auburn, Washington in the Greater Seattle Area. Established in 1997, Vision X Lighting’s products have consistently astounded customers with their lighting’s ability to perform in harsh environments and unbeatable light output. The engineering, product development, and marketing are conducted from the Vision X USA office, while Vision X Asia is home to the manufacturing, testing, and inventory logistics departments of Vision X Global Lighting. Today, Vision X Lighting has strong partnerships spanning across the globe where they continue to develop the most advanced lighting products in the world.
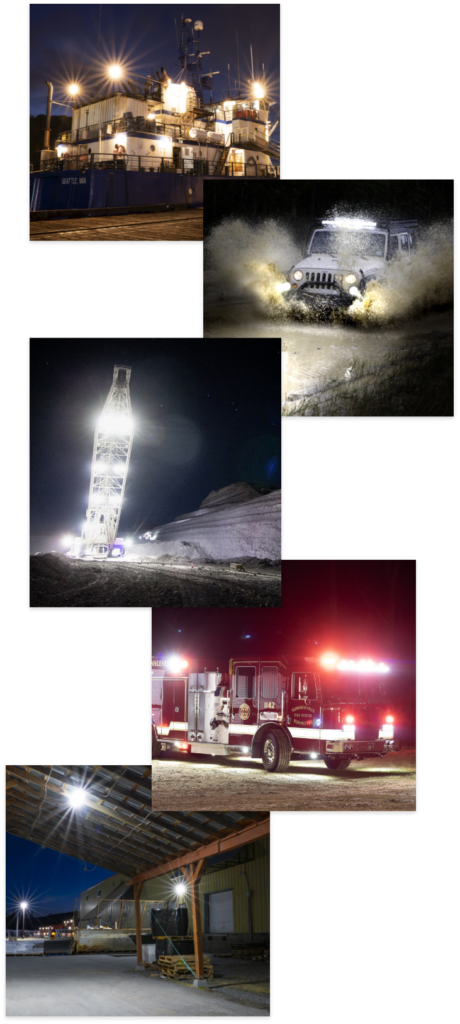
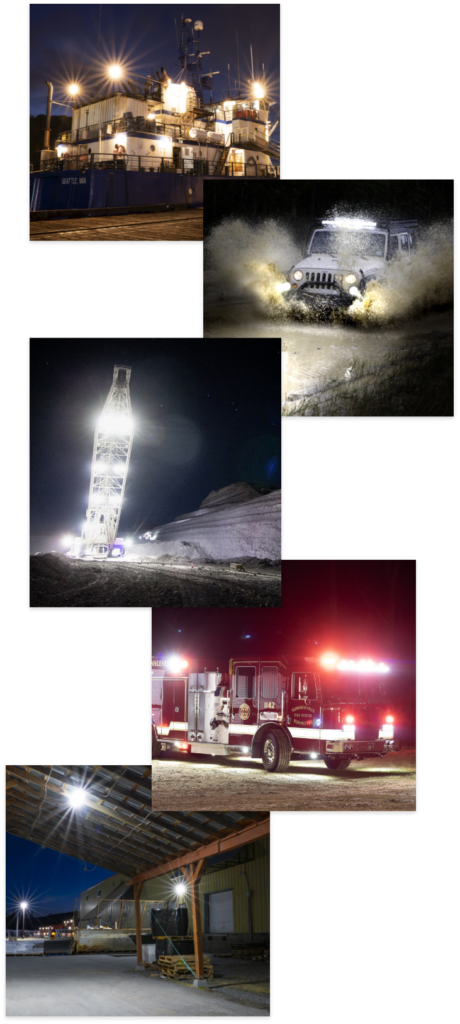
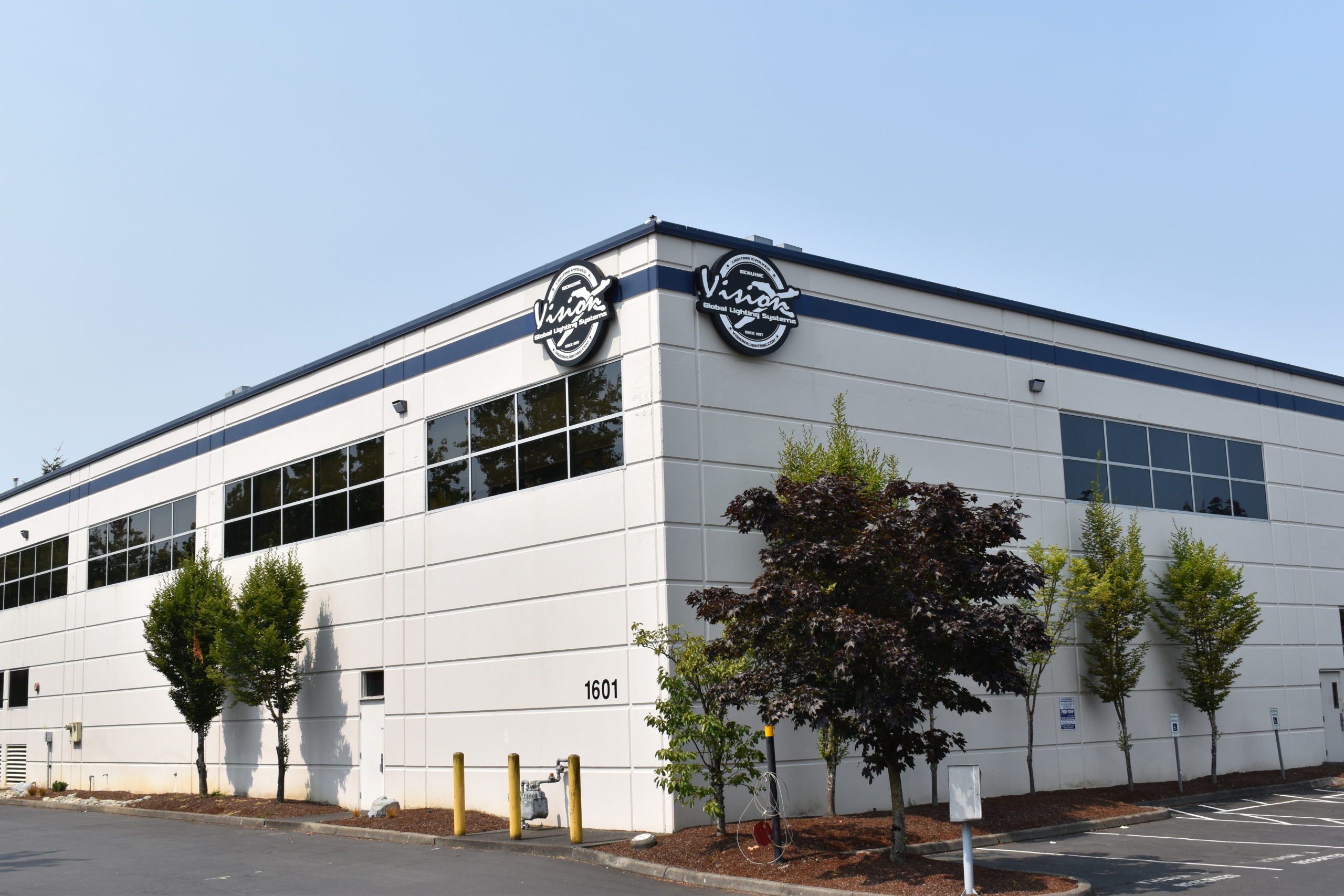
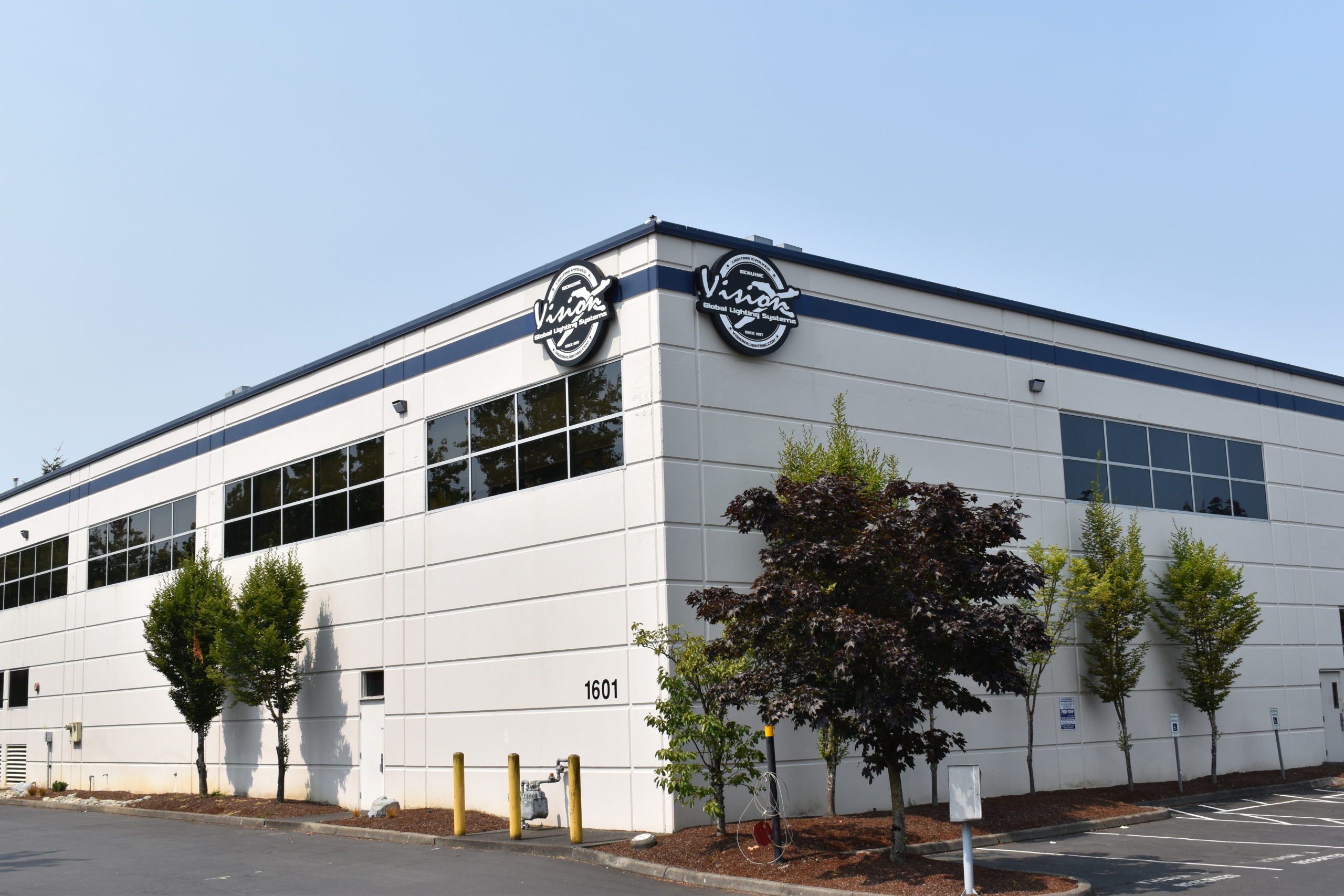
Key Markets
The Vision X product line is diverse and has products available for all markets. The military, industrial mining sites, commercial vessels, fire departments, and even NASA have trusted Vision X on equipment that doesn’t have the luxury of second-guessing their lighting. Our LED lights can be found on off-road vehicles, UTV/ATV’s, and even street-legal cars and motorcycles. Our key markets include:
- Mining
- Commercial
- Fire & Emergency
- Automotive
- Off-Road
- Marine
- Construction
- Forestry
- Agriculture
Lighting Evolved
Don't Take Our Word For it.
Quality as a priority
The Key to Vision X’s ongoing success, unmatched quality, valuing customer input, and performance is our team of world-class engineers who have taken outlandish concepts from conception and put them into production. Our engineers are never afraid of re-examining products to find ways to better serve customers. Since its conception, Vision X has listened to the end-user and put their ideas into action to further the quality, performance, and functionality of all Vision X products. Vision X Korea is our cutting edge manufacturing and testing facility, as well as, a shipping and account management hub for the eastern hemisphere.
Rigorous testing
At Vision X, our products are constantly improving due to our rigorous product testing and standards we hold our products to. Our lights have been tested using the most rigorous tests available, including by NASA in their TORR Chamber. Through these tests, Vision X ensures the best lights possible are on the market.
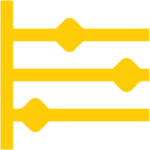
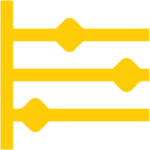
Consumption
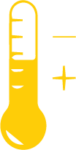
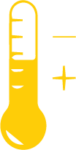
Thermal Impact Rapid Temperature Change
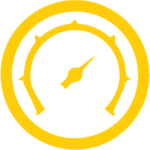
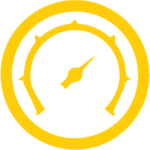
Ingress High-Pressure IP69K
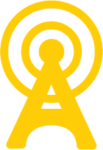
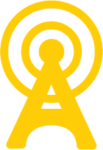
EMI
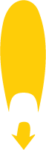
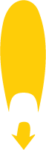
Photometric Isolux Beam Pattern
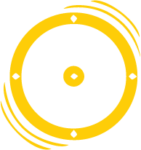
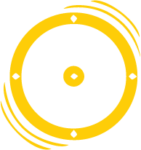
Vibration Rating
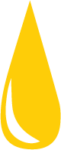
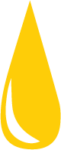
Submersion | Aging
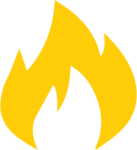
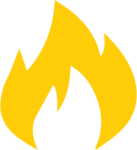
High Tempperature & High Humidity Operational
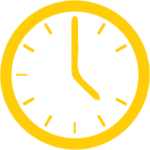
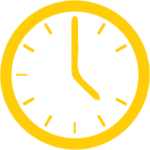